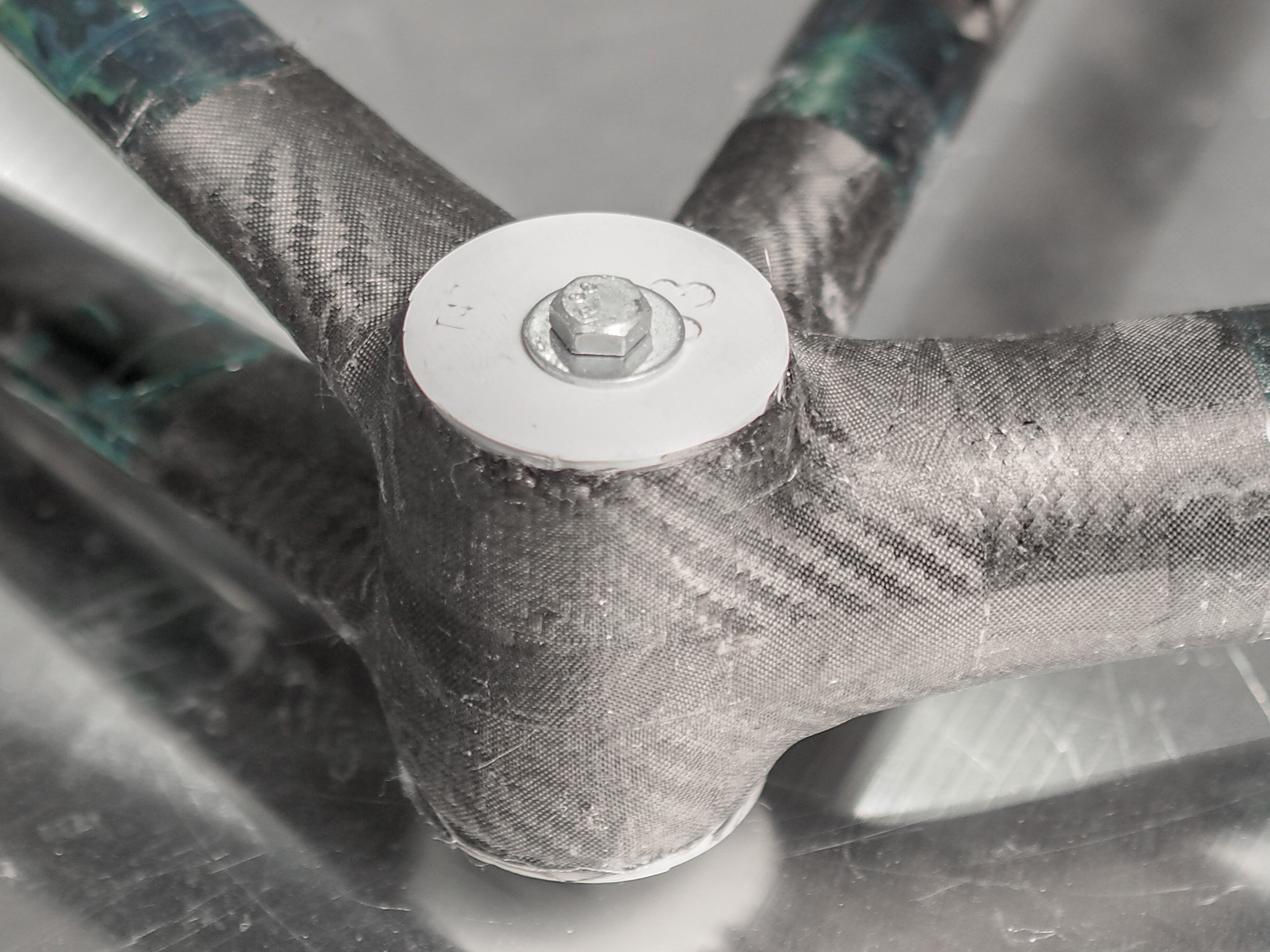
Process. Tube-to-Tube
Once the tubes are wound and the dropouts are molded, they are joined and reinforced by hand. 3D printed templates are extracted from CAD, and each tube is cut and mitered to length with tungsten-carbide tools. The mitered tubes and dropouts are reinforced with structural adhesive, filleted for smooth transitions, and then wrapped with layers of uni-directional and woven fibers. Once wrapped, the frame is vacuum-bagged and oven-cured. This is the most labor-intensive part of the process, requiring several cure cycles, as well as sanding and shaping, pattern cutting, and the careful hand layup of wet carbon fiber.